
Quality
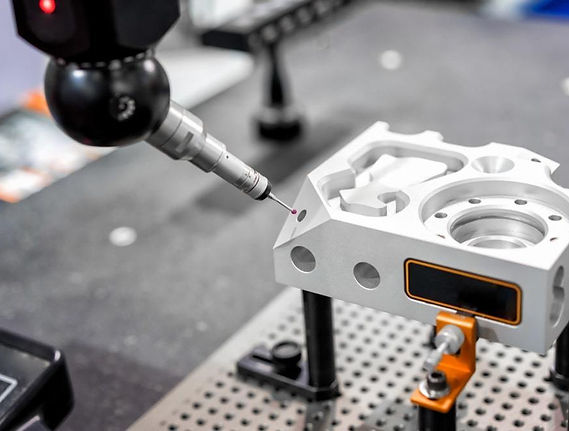
How Does JGM Manufacturing Ensure Quality Parts?
​
To ensure we deliver quality products right the first time, we’ll establish a robust quality management system with a focus on preventive measures. This includes setting clear quality standards and utilizing Six Sigma principles to identify and eliminate process inefficiencies. By carefully monitoring each stage of production with tools like statistical process control and maintaining strict adherence to specifications, we’ll minimize errors and rework. Regular inspections, calibration of equipment, and employee training will support consistent quality output, ensuring products meet or exceed customer expectations on the first pass.

Supplier/Subcontractor Quality Requirements
​
Vendor scorecards are excellent tools for assessing and managing the quality of your vendors. By tracking supplier performance against specific metrics, you can ensure they meet the quality standards your company requires. Here’s a structured approach to managing vendor quality using scorecards:
1. Define Quality Metrics and Expectations
-
Identify Key Performance Indicators (KPIs): Metrics like defect rate, on-time delivery, adherence to specifications, response time to issues, and continuous improvement initiatives should align with your quality standards.
-
Set Clear Expectations: Create a Supplier Quality Expectations (SQE) document that outlines your requirements and scoring criteria for each metric. Include guidelines on communication standards, quality control processes, and compliance with industry regulations.
2. Scorecard Development
-
Design the Scorecard Format: Include fields for each KPI, assigning weighted scores based on their importance. Weighting helps focus on critical factors impacting product quality.
-
Frequency of Scorecard Evaluation: Determine how often scorecards will be completed (e.g., monthly, quarterly), as consistent reviews provide better tracking over time.
-
Include Qualitative Assessments: These can cover areas like a vendor’s responsiveness, proactive issue-solving, and support during quality investigations.
3. Data Collection & Analysis
-
Collect Performance Data: Gather data from quality inspection records, delivery logs, and internal feedback to populate scorecards.
-
Analyze Results: Track trends to identify vendors with consistent issues or improvements. A scoring threshold can help decide when corrective actions are necessary.
4. Vendor Feedback and Improvement
-
Hold Performance Reviews: Share scorecard results with vendors, highlighting areas for improvement and recognition. Include a corrective action plan for any KPI deficiencies.
-
Implement Improvement Plans: For vendors not meeting expectations, work with them on improvement plans. Using a structured approach like Six Sigma DMAIC (Define, Measure, Analyze, Improve, Control) can help streamline improvements.
5. Integrate Scorecard System in ERP or Tracking Tool
-
If you’re building an ERP, incorporate scorecard tracking to store historical data and generate automated reminders for evaluations. This can also help identify vendors who are consistent high performers or at risk of replacement.